AUTOMOTIVE
- Home
- AUTOMOTIVE
The automotive industry is heavily invested in making sure that their products are safe, profitable, environmentally friendly, and appealing to their customers. Common challenges associated with these goals include achieving an acceptable time to market, finding ways to reduce cost while improving performance, and needing to validate new materials that, more often than not, have never been used in automotive applications.
The development cycle of vehicle design and manufacturing includes virtually endless decision-making opportunities where the consequences of making wrong decisions often result in obstacles that prevent manufacturers from meeting their goals. Instron provides automotive engineers with the tools needed to gain insight into material and part performance, helping auto makers receive accurate test data and product feedback throughout the entire design and production process so that they can make the most well-informed decisions possible.
KEY CONSIDERATIONS
When Selecting a Testing System for Automotive Applications
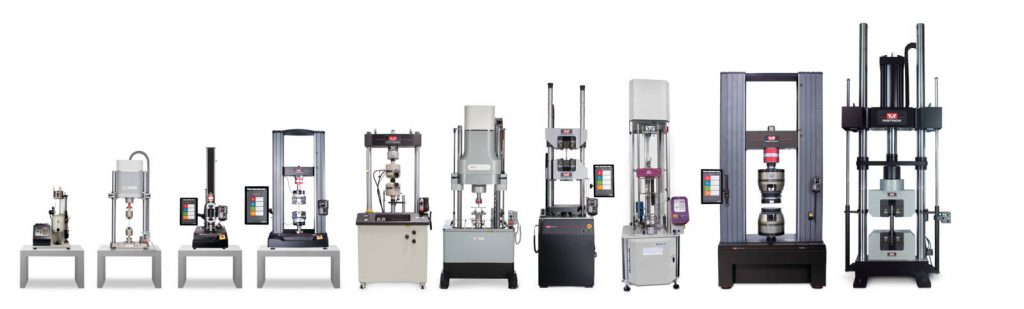

Reliability
Our customers can be confident in their investment: The average age of Instron systems on service contract is 18 years.

Repeatability
From load cells to extensometers, Instron makes its own sensors to ensure optimum system performance.

Application Expertise
With dozens of members on standards committees such as ASTM and ISO, Instron stays at the forefront of application expertise.

Versatility
With thousands of available accessories, users can easily interchange and adapt their systems to meet any new testing requirements.

Ease of Use
Instron customers trust that any new system is intuitive and easy for operators to use, regardless of skill level or application.

Global Presence
Instron sales and service are located in every region, representing 160 countries and 40+ languages.
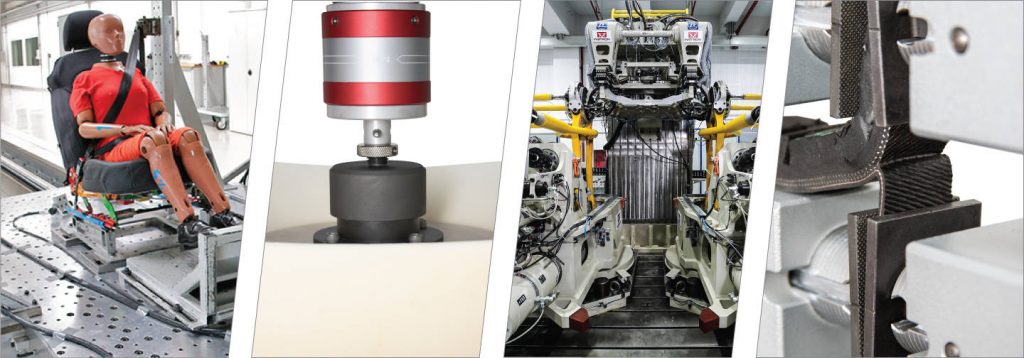
COMMON APPLICATIONS
- Electric Vehicles
- Wheel and Tire
- Chassis and Body
- Drivetrain and Suspension
- Electronics
- Engine
- Interior
- Joining
- Safety Systems
Electric Vehicles
The growth of electric vehicles (EVs) has brought new materials and components into the global automotive supply chain that require mechanical testing. To offset the immense weight of EV batteries, a heightened focus has been put on the preexisting light weighting trend. Similar to conventional automotive testing, raw materials and assemblies specific to EVs, such as polymer films used for Li-ion battery separators and the packs they ultimately form, require development and production testing.
Wheel and Tire
Wheels and tires are safety-critical components that are exposed to serious loads and wear over their lifetime. Their reliability can only be safeguarded by performing tests which resemble actual loading conditions as closely as possible, as well as obtaining a full mechanical profile of the materials being used for their production.
Chassis and Body
Traditionally the majority of an automobile is manufactured from various type of metallic material. The demand for more lightweight materials has meant a huge amount of research and development is now providing higher and higher grades of metals. This can bring many new testing challenges.
Electronics
Automobile manufacturers are constantly increasing the number of electrical assemblies inside their vehicles. With broad applications from on-board diagnostic computers, fuel injection systems, auxiliary lights, dashboard controls, and the increasingly-common infotainment systems, it is critical that all of these systems are tested to ensure quality and safety.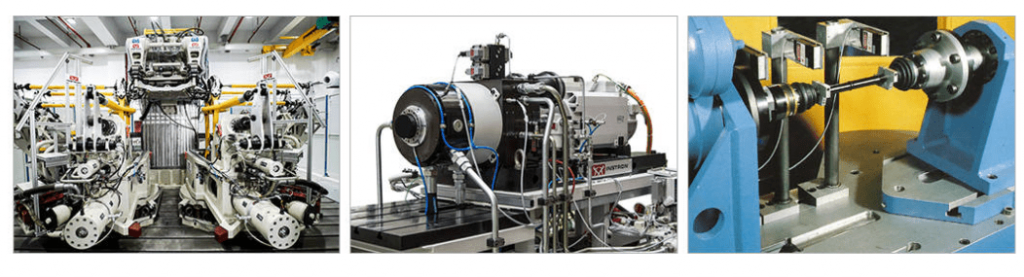
Drivetrain and Suspension
A vehicle’s drivetrain and suspension are some of its most vulnerable components. Depending on the part affected, damage can have a minor effect on appearance or lead to a major failure in vehicle safety. Both vehicle manufacturers and OEM part suppliers must comply with strict safety standards in order to produce high-quality components that make these systems as resiliant as possible.
Engine
It is important to be aware of how materials behave at ambient temperature as well as at their expected normal operating temperatures. Many OEM’s have unique temperature requirements that all components need to achieve; however, engine and transmission components get considerably hotter than the normal operating temperatures experienced by other parts of the vehicle. It is extremely important to subject the material being used for engines and transmissions to high-temperature testing to understand their performance under these conditions.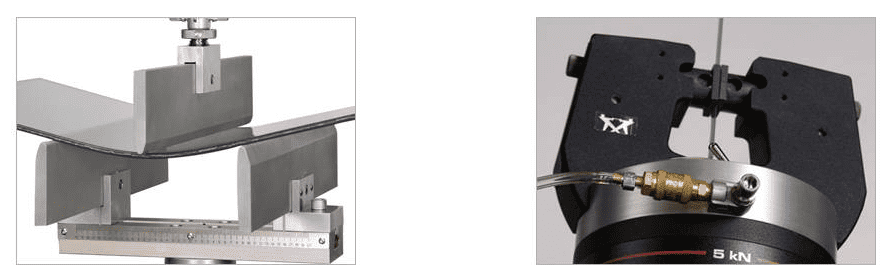
Interior
Automobile owners will see the interior of their vehicle every time they enter it, so the importance of aesthetics cannot be overstated. However, interior components must also be durable enough to withstand years of use. Mechanical testing of interior fabrics and components is necessary in order to ensure their long-lasting good looks and durability.
Joining
As the drive for lightweighting increases the range of materials used in automobiles, it becomes increasingly important to find reliable ways of joining these new materials together. Adhesives, fasteners, bolts, and welds are all vital to the overall construction of a vehicle. Knowing how these will perform throughout the lifetime of the vehicle is critical.
Safety Systems
Passenger safety is of the utmost importance in vehicle design, and the drive to improve safety fuels significant research and development. Mechanical testing is required to validate design and material selection. These tests then need to be implemented in quality control procedures so that each critical component is tested.
RECOMMENDED TESTING SYSTEMS
For Automotive Applications